Thanks to the interchangeable design gearbox provided by ABS and MGS Gears, Cementos Argos will not have to modify its original anchoring system. Only installing the electrical, pneumatic power connections and the clutch disc will be necessary.
Repowered Gearbox for Cementos Argos RD Main Mill Drive
Operation Background
Cementos Argos is the number one cement and concrete producing company in Colombia, and one of the most relevant in this sector in the United States, the Caribbean, and Central America. In operation in the Dominican Republic since 1996, actively participating in some of the country’s most emblematic infrastructure projects. For some time now they have been making important improvements to its KHD ball mill.
Changes were made to the internal diaphragms, dust collectors, gas recirculation, and peripheral devices, such changes made possible an increase in efficiency from 60 tph to 90 tph. The aforementioned modifications have progressively pushed the original design past its limits, causing major failures and negatively affecting its operation.
The Case
Since installing the 60 Tph KHD ball mill in 1999, Cementos Argos had a history of cyclical problems of failures in the primary drive. After a detailed analysis consequential to these problems, ABS proposed replacing four philadelphia single-stage reducers and a 2-stage Flender H2SH17 reducer as a solution.
Technical Solution
To minimize costs associated with modifications requiring a prolonged outage of operation, ABS and MGS Gears provide customized design and manufacture solutions, 100% interchangeable as well as repowered. All of which adapt to the mill’s original configuration regardless of their antiquity.
In this case, due to the limitations and restrictions of the main drive (clutch, motor, and slow rotation system) foundation, the proposed solution could not modify the original position of the engine or clutch.
Original dimensions of the foundation had to remain unchanged, same initial Flender H2SH17 gearbox input and output shaft lines and diameters and pneumatic power connection of the EATON double drum clutch.
Given the suboptimal condition of the gearbox, the solution called for an increase of the gears. ABS solved this situation through a unique design of superimposed intermediate stage that maintained the same input and output lines. This design increased the service factor from FS 1.7 to FS 2.6.
To optimize maintenance, ABS also replaced the lubrication unit for a dual-filter, dual-drive lubrication system with both stand-by and operation pumps working in parallel, making it possible to perform routine maintenance without a stop in production via the bypass system which blocks the flow.
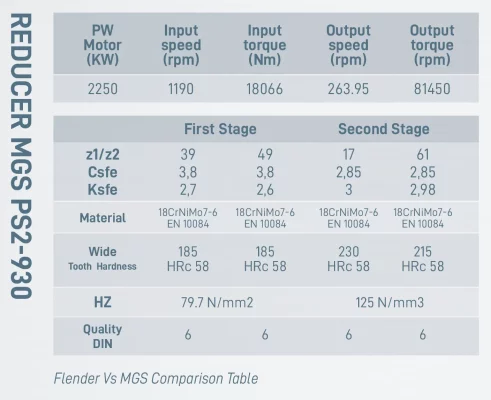
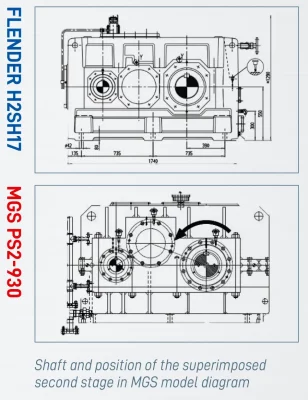
Another success story
Thanks to the interchangeable design gearbox provided by ABS and MGS Gears, Cementos Argos will not have to modify its original anchoring system. Only installing the electrical, pneumatic power connections and the clutch disc will be necessary.
Additionally, the reducer incorporates an improved coupling, temperature sensors capable of monitoring working conditions to which it will be subjected, and electro-welded housing made of increased rigidity steel and stress relief treatment to guarantee the most extreme operating conditions.
Download it in Newsletter format
ABS and MGS GEARS, Technical Excellence for the Heavy Industry
For over 20 years, we have been offering products and engineering solutions for all types of industrial applications drives such as Ball Mills, Rotary Dryer Furnaces, Bucket Elevators, using gearboxes and components capable of adapting to any assembly requirement, space availability, and required torque and ratio, etc. We count on a wide range of special bearings and power transmission solutions for the CEMENT industry to help optimize your production processes and extend the life of your industrial equipment.”