After 5 days of intense precision work and close collaboration with the plant’s technicians, the ABS and MGS teams made it possible for Cementos Santo Domingo to resume normal operation thanks to a newly installed girth gear with a 30-year operation life.
Cementos Santo Domingo is operating at full capacity with the new Girth Gear installed by ABS & MGS GEARS
Operation Background
Cementos Santo Domingo, S.A., specializes in the grinding and shipping of cement for use in the construction sector. The plant has a Portland-type cement milling process, possible through an Allis Chalmer Ball Mill composed of two chambers 3.35 m in diameter and 9.75 m in length with an 80 Ton/h capacity. The existing girth gear, manufactured by Falk had been used prior to being installed at the Cementos Santo Domingo plant, wear was present as a result of prior operation period. At the beginning of the year 2000, it was necessary to flip the girth gear to use its unworn face in order to complete the gear life of 20 years of operation.
Technical Solution
Using the pinion shaft the client had available as a baseline, the GIRTH GEAR was manufactured in 2 sections with an electrowelded structure. The outer ring is made of quenched and tempered forged steel to guarantee a hardness equivalent to 240-270 HB and has undergone ultrasonic testing.
Additional Challenges
The state of emergency resulting from the COVID-19 pandemic and restrictions on international travel proved challenging for the execution of this project. It was necessary to make different itinerary changes to complete the installation during the year-end holidays.
Girth Gear specification
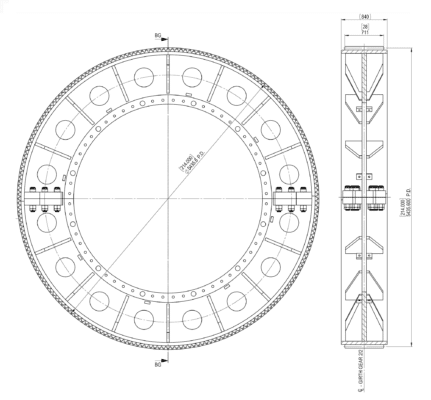
TOOTH QTY | Z1 | 216 |
MODULE | m (‘‘) | 1,005 |
PRESSURE ANGLE | * | 20 |
ELIX ANGLE (RH) | * | 7.30 (rh) |
FACE WITH | * | 28’’ |
WORKING SPEED | n2 (RPM) | 0.24 |
PINION TOORH QTY | z2 | 19 |
Installation
After disassembly of the Falk gear (previous), controls, cleaning, and preparation of the flange is performed to ensure alignment between the gear and the mill are within recommended parameters. Once the two sections were installed and the Superbolt screws are set in place, the flange screws were adjusted and several corrections were made to the alignment using a calculation program designed to make adjustments in specific correction points,thus achieving a maximum axial deviation of 0.035 and 0.040 radial deviation. After girth gear is centered pinion-gear alignment is performed using gages to fix tooth position and necessary adjustments to the mill’s drivetrain are carried out. To conclude the installation, the lubrication system was tested, and a lubrication and load application protocol was created so that loads are gradually applied, starting at 60% until a maximum load of 100% is reached while monitoring vibration,temperature, and lubrication efficiency.
ABS & MGS GEARS technical service offer
ABS and MGS Gears teams count with extensive experience to offer practical solutions for all types of industrial drive applications such as Ball Mill, Rotary Kiln, and Bucket Elevators among others that utilize gearboxes and drive components while adapting to installation requirements, available space, and power and ratio requirements.